Background
The proposed Harris Academy School, Purfleet was to be located within a heavily industrialised part of Essex. Sanctus took control of the ~2.3ha site following the demolition of previous warehouse structures, leaving expansive concrete slabs, exposed Made Ground and dense areas of vegetation across this sprawling industrial site. The site is bound by residential housing to the north west, the River Thames runs <100m south of the site and other industrial units to the east.
Numerous contaminants of concern, including lead, asbestos and petroleum hydrocarbons were encountered during previous investigations of the site. The site had been earmarked to provide a location for the much-needed new secondary school with associated car parking, soft landscaping, sports and multi-use games areas. To make this vision possible extensive and site wide remediation was required, the concrete slabs and subsurface obstructions were to be broken out and the resulting material crushed, tested and re-used on-site.
A detailed cut/fill design was developed and adhered to with the import of suitable material to site to achieve final required levels. There were numerous technical challenges through which Sanctus were able to identify many opportunities:
•Approximately 20,000m2 of the site was covered in heavily reinforced concrete which required breaking out, crushing, testing and placement.
•A detailed cut/fill model was necessary to leave the site at the correct profile for the following contractors and ultimate end usage.
•A shortfall of materials was identified so additional, suitable materials were required to achieve design levels, as well as creating the correct import mechanism.
•Perched groundwater was encountered across site at shallow depths and at large volumes which required careful management.
•Heavily contaminated water required sensitive management, pumping and treatment, prior to re-use as dust suppression as and when required.
•Free phase hydrocarbon was observed within a perched water trial pit necessitating the pumping and treatment of impacted groundwater.
•The requirement to treat contaminants on-site necessitated the deployment of Sanctus’ Mobile Treatment Permit and significant associated regulatory liaison.
•Asbestos was identified across the site requiring asbestos controls (RPE & PPE) to be in place during works within the Made Ground.
•The project programme was extremely tight and of paramount importance to the client as second phase of contractors were booked immediately following Sanctus’ works.
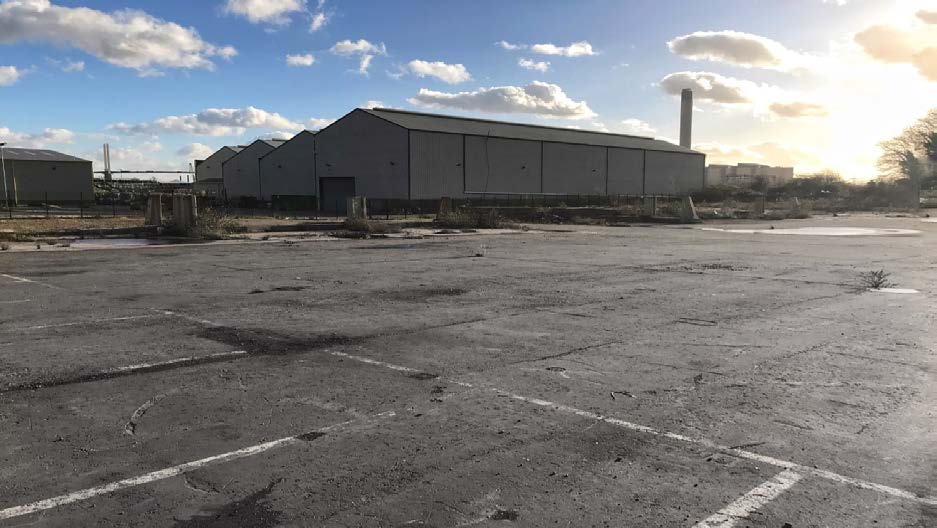
Innovative Thinking and Exemplary Best Practise
The site was almost fully covered in heavily reinforced concrete which needed to be removed to initiate the programme of work.
The conventional approach would see multiple excavators equipped with hydraulic breakers, a costly, fuel and labour intensive as well as environmentally impactful and relatively slow process, which was estimated at circa three weeks creating a huge amount of noise, dust and vibration in the process.
In many ways presenting all the additional environmental impacts you would wish to avoid or mitigate where possible during remediation works.
The large lateral extent of hardstanding meant the use of a multi-head breaker was a viable option. The self-propelled multi-head breaker carried 800kg hammers, mounted laterally in pairs. The hammers were dropped in sequence from a set height, generating 30-35 impacts per minute. This pulverisation technique allowed for easier removal of the reinforcement, and swifter crushing of the retained materials, achieving the remarkable full break-out within three days.
To reduce costs and environmental impact, all crushed hardstanding was tested and re-used on-site. Apart from non-site compliant recyclable metals and handpicked asbestos fragments, no materials were removed from site, with all soils, concrete, and water being managed, processed, treated, and tested to facilitate onsite reuse.
As well as providing significant financial savings, the re-use of materials reduced impact on the environment through minimising offsite disposal and the use of finite landfill void, a reduction in the overall carbon footprint for the project and eased associated traffic around site and beyond.
Processed material was tested to confirm suitability with one of three re-use criteria / location: under the building footprint, outside the building footprint and within the capping layer.
A temporary stockpiling area was established with material subsequently reinstated in line with its designated re-use classification. To warn future ground and maintenance workers of the potentially contaminated land a high visibility geo-textile was installed across the base of the capping layer.
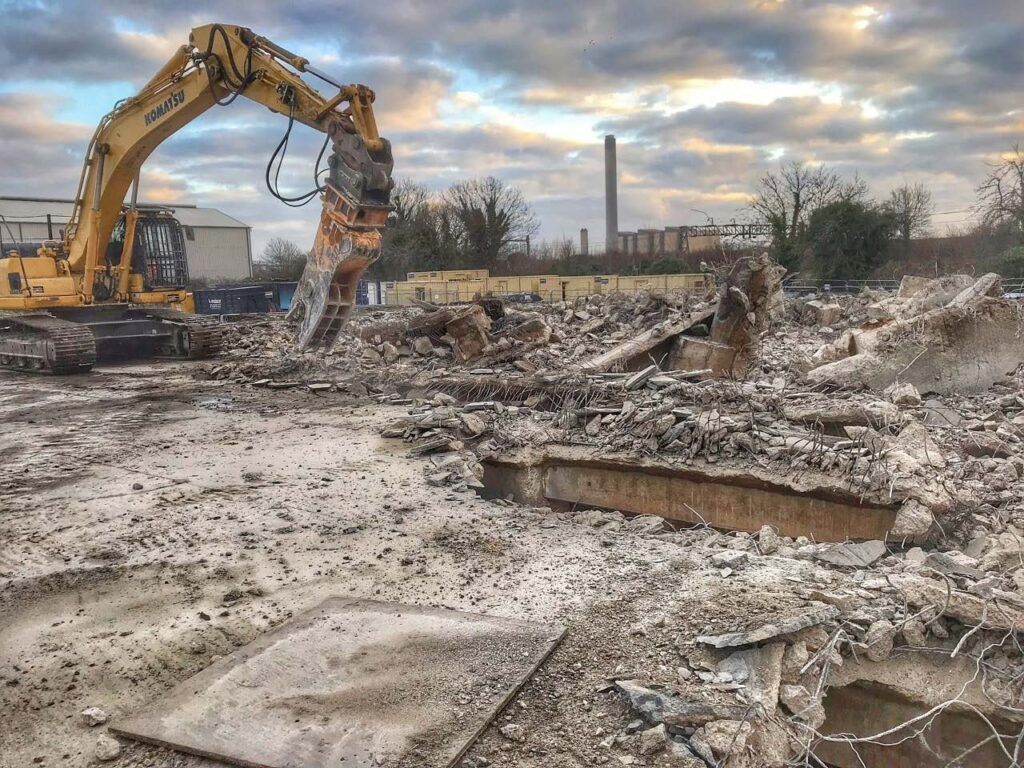
Licensing & Regulatory Liaison
All material re-use was in accordance with a suitably declared Materials Management Plan, written in accordance with the CL:AIRE Definition of Waste: Code of Practise.
Following the re-use of all hardstanding on-site, a shortfall of materials was identified to achieve the required formation levels. As such Sanctus utilised our local approved supply chain to source material from a licensed supplier to reduce environmental impact and in line with our social-responsibility principles, help support the local economy during all our work.
To facilitate the import of such materials the previously completed Materials Management Plan was revised to change the scenario and identify the site as a Hub Receiver Facility, this required extensive regulatory liaison and additional declaration by the independent Qualified Person, all of which was successfully undertaken prior to the import of any materials
Prior to importation, Sanctus undertook a site visit and conducted chemical testing to confirm suitability at the source. The material was found to be suitable and subsequently imported, thereby preventing the requirement to import virgin quarried materials further increasing the sustainability of the project.
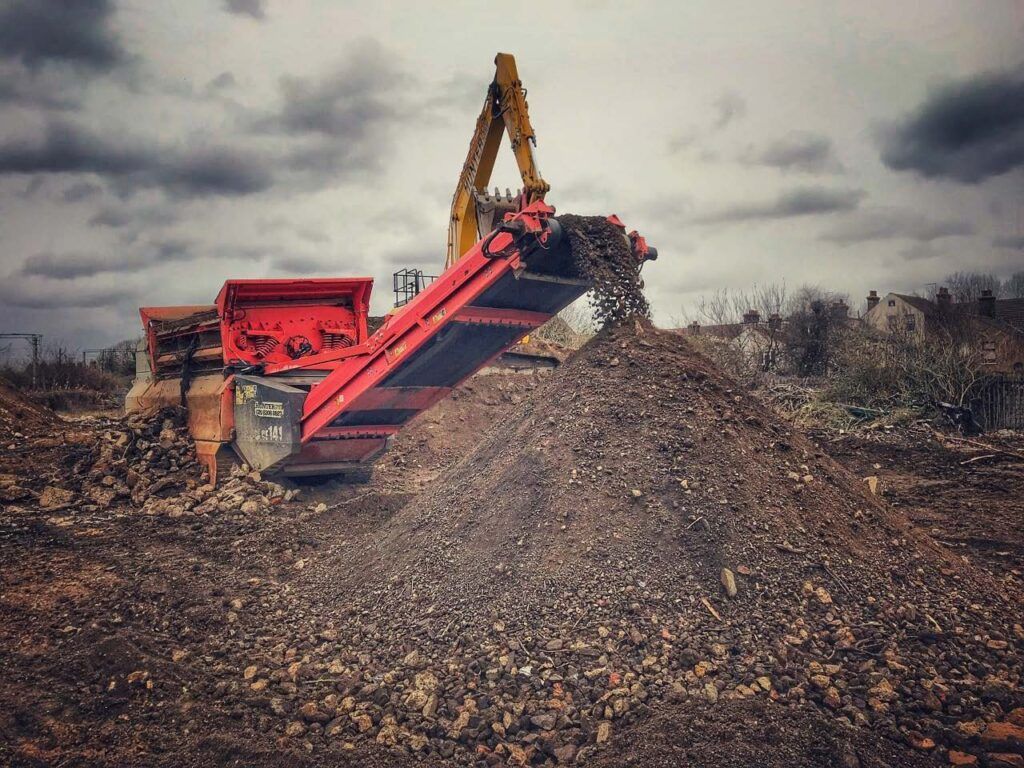
Asbestos Contamination
The principle contaminant of concern identified onsite was asbestos in both fibre and fragment form. An initial site investigation recorded 60% of the samples screened testing positive for asbestos. As a result of the nature and type of asbestos present the works were assessed as notifiable non-licenced works (NNLW). All works involving asbestos were carried out under suitable controls in accordance with the Control of Asbestos Regulations (CAR, 2012) and Sanctus’ HSE issued License to undertake work with asbestos.
One existing stockpile inherited with the site was found to be heavily impacted with asbestos fragments. A conveyor belt system was utilised to feed the impacted soil through a picking station where visible asbestos fragments were handpicked along with any deleterious material. The handpicked materials were sent to a specialist asbestos disposal facility and the processed soil reinstated on-site.
Removal of Buried Obstructions
To facilitate the removal of subsurface obstructions a significant programme of dewatering was required. Abstracted groundwater was pumped through a bespoke water treatment system. The system comprised an oil / water separator, water clarifier and carbon pod. This water, following treatment, was reused for dust suppression to reduce the demand on the environment of both dust and additional water extraction.
Portable oscillating point source suppression methods were utilised to prevent dust generation and a perimeter misting system was also deployed around the boundary of the site.
A 150mm layer of free phase petroleum hydrocarbon contamination was encountered on the perched water within trial pit. The trial pit was extended along service corridors in accordance with the Remediation Strategy to identify lateral extent of the contamination. An oil-water interface probe was utilised to measure the thickness of free phase hydrocarbons present within the excavation resulting in the need to deploy a surface skimmer to effectively remove the product. The impacted water was pumped into an 600litre IBC until no visible sheen was present. The IBC was subsequently removed from site to a licenced disposal facility under the necessary duty of care.
Hydrocarbon impacted soils were excavated and stockpiled in a 1m high 2m wide bund. The bund was placed upon heavy gauge polythene to prevent vertical migration of leachate. The material was mechanically turned and aerated to enhance volatilisation and natural degradation of the petroleum hydrocarbons present. The excavation remained fenced, displaying the appropriate signage until the excavated material exhibited no visual or olfactory evidence of hydrocarbon contamination. The material was subsequently backfilled and compacted in accordance with the specification
The development required piled foundations as the foundation solution. To monitor the impact of these piling operations on groundwater chemistry, groundwater quality monitoring was undertaken before, during and after the piling works across three boreholes. No adverse impact was identified as a result of the piling activities. Ongoing environmental monitoring was conducted for the duration of Sanctus’ works on-site. The monitoring was conducted across six locations around the perimeter of site, with odours, dust, litter and noise levels recorded with action plans in place if exceedances were noted.
Public and Stakeholder Engagement
We take huge price in our commitment to public engagement and inclusion believing that our projects are ultimately designed to benefit people and the environment. Surrounding businesses and residential properties were consulted prior to work beginning based on the principle of listening to understand not just listening to respond.
As pulverisation and the crushing processes produced both noise and vibration, work directly adjacent to neighbouring businesses was scheduled and undertaken during breaks in their manufacturing process so not to disrupt their works. Site hours were also moderated and adjusted as not to disturbed surrounding residential properties. The relationship between site staff and neighbouring businesses was typified by friendships developing between members of the community and the Sanctus team and highlighted by the Sanctus Site Manager adopting two retiring guard dogs following completion of work on site.
Economic, Environmental and Additional Social Benefit
We believe in returning lost spaces and forgotten space to people and the environment. This project has been a catalyst for social mobility, diversity and inclusion within and beyond Purfleet.
Purfleet is a highly industrialised area in the process of building a new future, the development of a state-of-the-art academy with world class sports pitches has helped give new ambition and inspiration to the area’s young people.
The need for such a facility is evident as the first intake for the academy was fully subscribed ahead of the building’s completion.
The academy is located in the heart of the community and will help improve education, wellbeing and inclusion as well as providing clear social and economic benefits for the local community and beyond.
We’re incredibly proud of our work at Purfleet and look forward to watching the area grow from strength to strength.